Lean
expertise
Lean management helps organizations work as efficiently as possible by preventing waste. Consider, for example, work that does not directly add value for the customer.
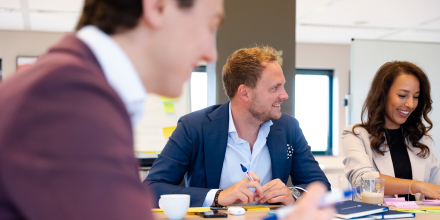
Why Lean?
Lean management is fully developed with the customer at its center. By putting customer needs first, inefficiencies can be identified and addressed early. Lean utilizes a “pull” system, where production and operations occur only when there is demand. This ensures continuous flow and strives for perfection through small, incremental improvements. The result? Improved quality, reduced project time and lower costs.
How to work lean
Lean-principes
But how do you make an organization Lean and how does it work? This is only possible if the entire organization shares the same mindset and consistently works according to Lean principles. These principles form the backbone of all activities and decisions within the organization.
By embracing Lean, everyone focuses on creating maximum customer value, eliminating waste, and continuously improving processes. Implementing Lean requires commitment and dedication from all employees, as well as a culture of collaboration and continuous innovation. Only then can Lean really come into its own and take the organization to the next level.
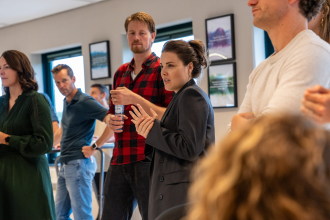
Puntsgewijs
-
Value
Value is all about putting the customer first. It is essential to always create as much value for the customer as possible.
-
Value stream
The value stream is about mapping current processes and activities and identifying which of these add customer value and which do not. This can be done by conducting a Value Stream Map.
-
Flow
Flow focuses on eliminating found waste, leaving only the activities and process steps that add value.
-
Pull
Pull means that when waste is minimized, products are produced only when the customer requests it. This prevents new waste.
-
Striving for perfection
This principle revolves around continuous improvement. The organization does not have to be perfect, but it must constantly strive to improve and learn to become a little better every day.
Various levels of Lean
Within Lean, there are different grades at the management style level, denoted by colors, similar to the belts in judo. The levels range from Yellow Belt to Black Belt. Just as a beginner in judo wears a yellow belt and an experienced judoka wears a black belt, the colors within Lean represent the level of knowledge and experience.
The different grades are:
- Yellow Belt
- Orange Belt
- Green Belt
- Black Belt
What is the difference between these levels? Each level represents a deeper knowledge and skill in Lean principles and applications.
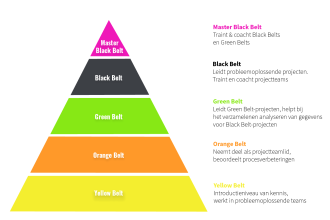
Lean levels
What are the differences between the different colors of belts?
Yellow Belt
The Yellow Belt lays the foundation for Lean by learning the fundamental principles and techniques. This level serves as a stepping stone to higher levels.
Orange Belt
After establishing a good foundation, you will advance to the Orange Belt. At this level, you expand your knowledge and learn how to apply it in practice.
Green Belt
The focus is on working together effectively within a project team. You will learn how to apply learned theory to larger project groups to achieve successful results. In our Lean Green Belt training, all Belts are covered, giving you a solid foundation and allowing you to advance to the Lean Black Belt level. doorgroeien naar het Lean Black Belt niveau.
Black Belt
The final step in Lean training is the Black Belt. At this level, you will learn how to set up transition programs within a company and support Green Belts.
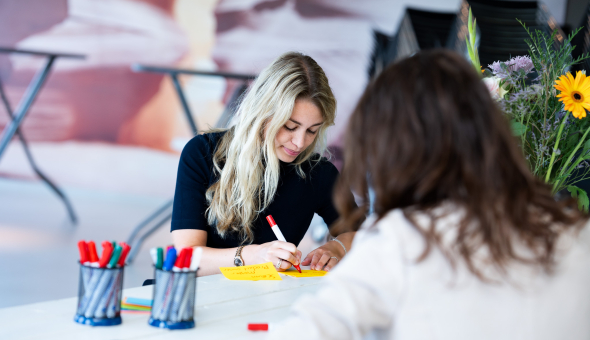
Lean trainingen
Would you like to learn more about Lean?
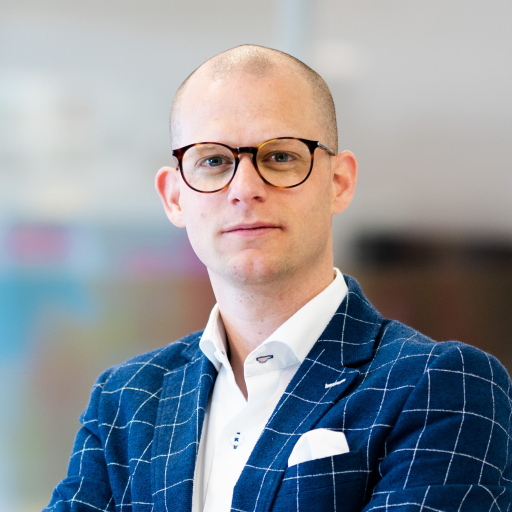